Cooperation and Consulting
Case Study 1 - Device-to-Device Mobile Communications and Stochastic Geometry
Company
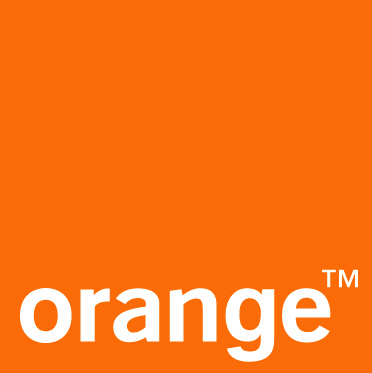
Orange S.A. is a major french telecommunication provider that globally operates mobile, landline, internet and television services. Dedicated teams at the Orange Labs research and development devision in Châtillon France perform fundamental as well as applied research on challenges and opportunities of dynamical device-to-device (D2D) communications in urban and rural environments.
Challenges
The ever increasing demand for fast and reliable data exchange in communication systems poses great challenges but also opportunities for network operators around the globe. One very important aspect here is the exponentially increasing use of mobile devices such as cellphones and communicating cars. This is also reflected in the 5G specifications, where faster connections, higher throughput, and more capacity are envisioned via an enhanced mobile broadband, and ultra-reliable low-latency communications should enable the system to support time-crucial applications such as car-to-car communication.
In this context, device-to-device (D2D) communications is considered one of the key concepts pervading a highly diverse set of use cases. On the one hand, D2D systems hold the potential to relief present day cellular networks from at least some of the system's pressure. On the other hand, D2D communications can provide for example faster and more robust connectivity. However, from an operator's perspective, D2D systems are much less controllable than traditional cellular network due to the dependence on the individual user behavior. This lack of control becomes even more severe, when the devices are mobile. Thus, in order to properly predict the performance of D2D systems, either with or without additional infrastructure, a detailed and comprehensive modeling and model analysis is imperative.
WIAS Analysis and Solution
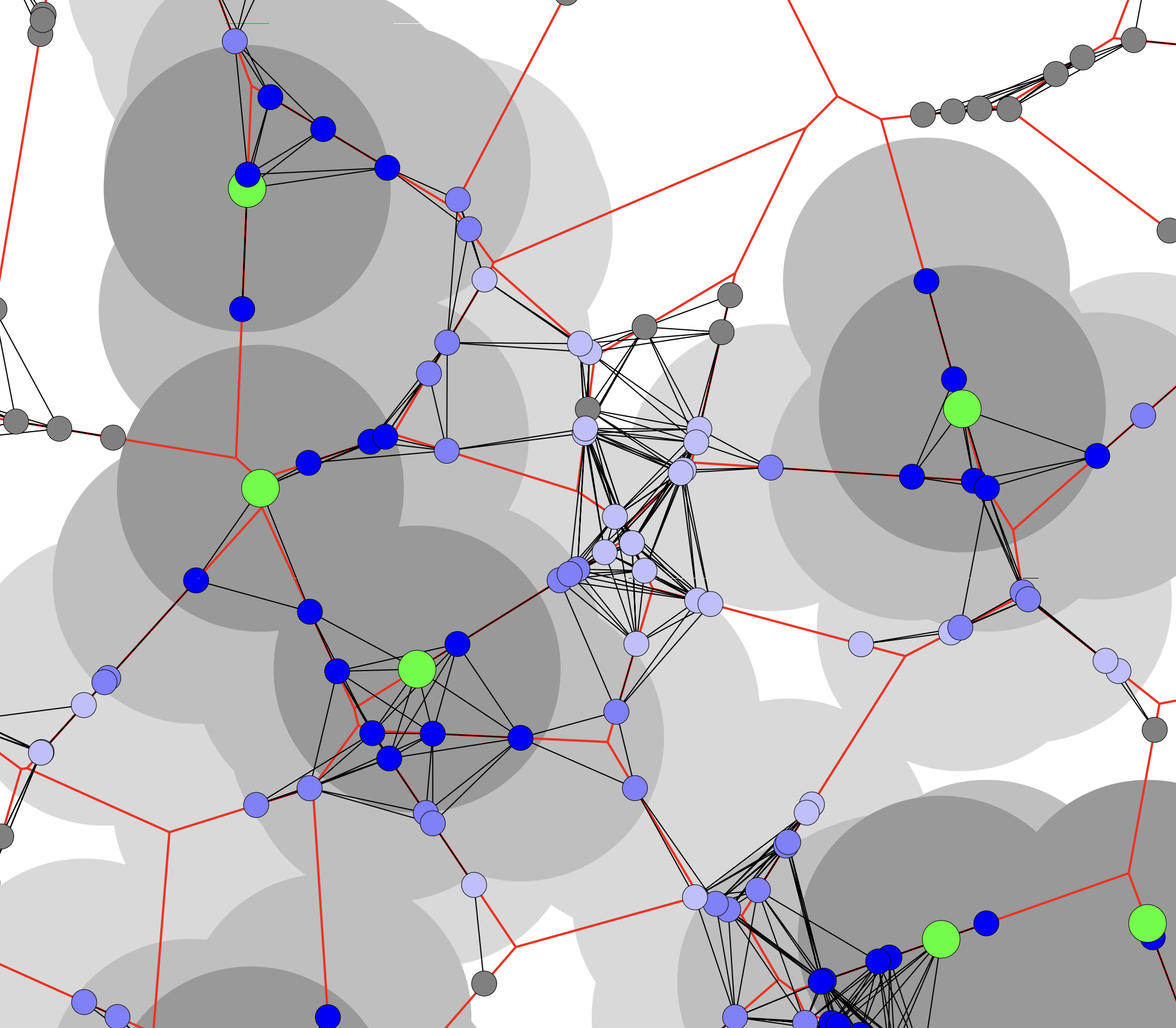
In view of the described challenges, a natural ansatz is to incorporate uncertainties of the system with the help of probability theory. The starting point is the modeling of random initial locations of the devices and their individual movements in cities or rural areas. Based on this, the transmission mechanism between any pair of devices has to be represented with a reasonable level of detail, for example not neglecting that the devices need to spend some minimal amount of time in close proximity. Ultimately, then the distribution of data through the D2D system over time can be analyzed, leading to predictions for examples for the connectivity, throughput, or more generally, the quality-of-service of the network.
The joint research of Orange Labs and WIAS started in 2016 with a one-year project on continuum percolation theory applied to D2D. This project analyzed the connectivity of a static D2D model of devices in urban environments communicating over long distances via a possibly unlimited number of relaying hops. Extending the theory of continuum percolation to Cox point processes paved the way towards estimates for the proportion of participants in a pure D2D network to guarantee good long-range connectivity. A closely related PhD project extends this connectivity analysis to scenarios with relays located also at crossings. Building on this expertise, the subsequent project on typical cells in anisotropic tessellations further studied the underlying street system with respect to the cell of a typical network component placed on a street. Here algorithms and software were established for the numerical analysis of Manhattan-type street systems failing to exhibit the rotational invariance deeply ingrained in classical tessellation models.
Over the course of several years, in a total of six projects, WIAS researchers further supported the team at Orange Labs on a diverse set of topics such as "data mobility in ad hoc networks and their vulnerability and security", where parametric connectivity models were derived in order to better understand how malicious software spreads within such a system in the presence of different countermeasures, or "coverage and mobility in device-to-device networks" where the focus was towards extending the coverage zone of a set of infrastructure nodes by restricting the number of relaying hops over other devices.
Conclusion
In the multiple joint projects with Orange S.A., the comprehensive expertise on stochastic geometric modelling and analysis at WIAS could help to further advance our understanding of peer-to-peer communication networks subject to various kinds of randomness. Contributions could be made on a fundamental level for example by developing a theory of percolation in random environments or interacting particle systems on random networks, but also with respect to applications for example by providing numerical estimates for critical parameters for long-range communications or decentralized malware elimination.
Case Study 2 - Crystal Growth in a Traveling Magnetic Field
Companies
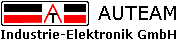
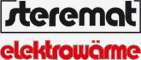
The two companies, along with WIAS and the Leibniz Institute for Crystal Growth (IKZ), formed a consortium that was funded for a period of three years by the federal states of Berlin and Brandenburg, as well as by the European Regional Development Fund (ERDF).
Problem
The most important production methods for semiconductor bulk crystals start at high temperature with a melt, and then the crystal is obtained on controlled cooling. During the so-called Czochralski process and its variants, the crystal is pulled from a rotating melt.
In order to achieve a homogeneous crystal, three requirements must be met: one needs, preferably, a spatially and temporally homogeneous temperature, a controlled flow within the crucible, and a convex interface between melt and crystal. The desired process up-scaling (increase of the production device in order to achieve larger crystals) leads to serious complications.
This new requirement calls for major changes in the growth device, and new experiments to determine the new optimal parameters become necessary. To be able to produce larger crystals with the same quality, one may even need some additional technical equipment. For example, traveling magnetic fields are successfully used to control the melt flow during Si growth. But the application of this new technology to the growth of III-V compounds leads to an unfavorable high power consumption, since the magnetic fields are typically generated by induction coils placed outside of the growth apparatus so that the thick walls of the pressure chamber significantly diminish the applied magnetic field.
WIAS Analysis and Solution
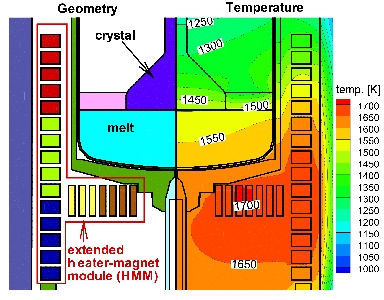
For the reliable and efficient mathematical simulation and optimization, a coupled system of partial differential equations on a complicated, nonsmooth cylindrical domain had to be solved. The scientific software tools WIAS-HiTNIHS and NAVIER were extended and applied to the numerical treatment.
Within the KRISTMAG project, the partners could show that an internal heater-magnet module can generate traveling magnetic fields that are able to control temperature, flow, and interface boundary in the favored sense. Several pilot devices have been manufactured, a couple of patents were filed and awarded. The groundbreaking nature of these developments was recognized by the Innovation Award Berlin-Brandenburg 2008.
Conclusion
The simulations performed greatly contributed to the modified system configuration and delivered optimized parameter configurations for its operation.
A resulting cooperation project between the same partners and other companies, dealing with controling the growth of silicon for solar cells from the melt by using traveling magnetic fields, has taken place.
Case study 3 - Evaluation of Dilatometer Experiments
Companies

The following example was part of a two-year project between WIAS, the Department of Ferrous Metallurgy at RWTH Aachen University and the Bähr-Thermoanalyse GmbH. It was financially supported by ZIM, a funding program of the German Ministry of Economics and Technology to support small and medium enterprises.
Problem
The starting point for this project was a mathematical result. In a joint fundamental research project with the Department of Ferrous Metallurgy of RWTH Aachen University funded by the German Science Foundation (DFG), we were able to prove that the complete phase transition kinetics for two growing phases can be uniquely identified from dilatometer measurements.
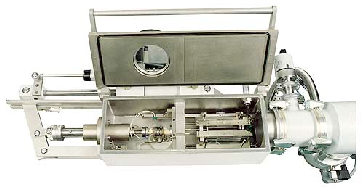
Such a dilatometer (see figure) is a device to measure the deformation and temperature evolution subject to controlled heating and cooling.
State of the art in dilatometer data analysis is that it is used solely to detect the transformation temperature for the onset and end of phase transitions. In the case of more than one phase transition, the detection of the final phase fractions up to now requires costly micrograph section analysis.WIAS Analysis and Solution
Since induction heating is not only used in the heating stage but also to realize slow cooling rates, the mathematical model includes thermo-mechanics and an eddy current formulation of Maxwell's equations.The phase kinetics can be computed from an inverse problem using a Gauss-Newton method. To obtain reasonable computing time it is indispensable to reduce the resulting model exploiting the symmetries of the problem.
WIAS Implementation
After one year an identification algorithm for the fast cooling has been developed and implemented. Experiments to validate the numerical approach were conducted at RWTH Aachen University.
In cooperation with the company, we have investigated ways to enhance the reliability of the solution to the inverse problem by a consequential use of all available experimental data.

Cooperation and Consulting
