WIAS-MeFreSim
Simulation of multi-frequency induction hardening
Developed by:
Our Software
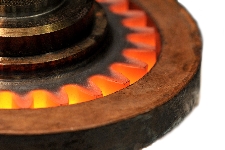
Background
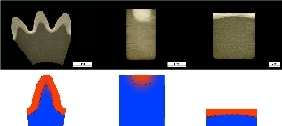
WIAS-MeFreSim is used for the simulation of induction heat treatment for workpieces made of steel. It is the aim of the heat treatment to produce workpieces with hard, wear resistant surface and soft, ductile core. The boundary layer of the workpiece is heated up by induced eddy currents and rapidly cooled down by the subsequent quenching process. The resulting solid-solid phase transitions lead to a hardening of the surface of the workpiece. The figure shows the comparison between experiment and simulation for a gear, hardening profile in cross section and lateral cuts of tip and root of the gear.
Features
- Determination of electromagnetic fields, temperature and the phase fraction profile in the workpiece and of mechanical stresses and deformations
- Determination of the physical fields by using adaptive finite element methods
- 3D-visualisation of results
- Extensible database for material parameters and transformation kinetics for various types of steel
- Experimentally verified simulation results
Our Services
- Individual consulting and realisation of simulations for the induction heat treatment
- Concerted further development including acquisition of public funding

Contact
Phone, E-mail
Tel.: 030 20372-498
E-mail: mefresim@wias-berlin.de

WIAS Software (Archive)
- awc - Adaptive weights clustering
- BOP - A Simulator for Large-Scale Process Engineering Problems
- ClusCorr98 ® for exploratory data analysis
- gltools for interactive or non-interactive graphical output
- WIAS-MeFreSim - 3D-Simulation of Multifrequency Induction Hardening
- WIAS-QW for the simulation of strained multi quantum well structures
- S/PHI/nX library for materials simulation
- WIAS-TeSCA for two and three dimensional semi-conductor analysis